Copyright © 2015, PT. Asia Enviro All Rights Reserved.
Please note that all logos, brands, trademarks, company name/names appearing in this website are trademarks or registered trademarks of their respective companies.
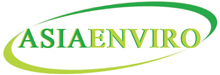
Reverse Osmosis is at present a proven technology in world desalination scenario and contributing bulk quantum in global consumption for various applications. Today the impressive demand for desalination has been a major thrust for improvement and refinement of this technology. The major problem with RO desalination plants and their application limitation is their susceptibility to fouling and scaling, the implications of which are usually irreversible membrane damage, reduced flux rates, & increased capital and operating costs.
Therefore selection of a proper module configuration available for Reverse Osmosis Membrane Applications is the crux of the issue. The selection of a particular configuration depends on their relative characteristics.
The following are the commercially available RO membrane configurations:
A. Spiral Wound Module (SW)
B. Hollow Fine Fiber Module (HFF)
C. Concord Enviro Plate-Frame (PF) Membrane Module
A) Spiral Wound
In a spiral wound module, the membranes are separated and a feed channel is produced by wrapping a piece of mesh spacer between membrane layers. This spacer (provides only approx. 3 micron spacing between membranes) creates a primary difficulty in the use of spiral wound modules. The mesh greatly reduces the amount of open flow area between membranes and acts as inline filter and traps suspended solids in feed stream. The spacer creates eddies and zones of zero flow where biological growth and fouling occurs in the module. Typically lengthy flow path of 40 inches and above results in build up of polarization concentration that increase scaling and fouling.
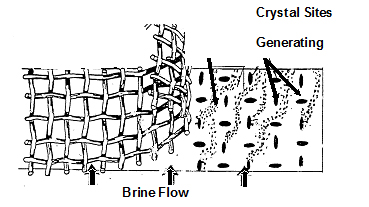
B) Hollow Fine Fiber
The hollow fine fiber modules have hollow fibers with approx. millions of hollow fiber capillary tubes pressed together which give even smaller channels for a continuous flow of water through that module, and results in build up of polarization concentration that increase scaling and fouling. Hollow Fine Fiber is having wider application in ultra-filtration.
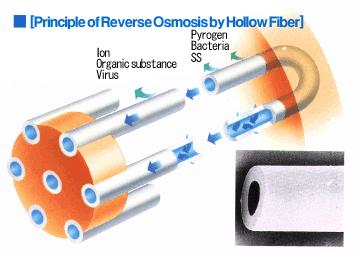
C) CONCORD ENVIRO Plate-Frame (PF) Membrane Module
The patented PF-MEMBRANE-MODULE is a modern design for molecular separation, desalination and purification of liquids. It can be operated effectively and economically at increased turbidity and Silt Density Index levels for reverse osmosis. The plate-membrane stack is assembled on the center tension rod with metal end flanges. The module stack is covered in an open, untreated, standard 8 inch pipe. The feed water is sealed by a pressure flange seal. The pressure vessel design allows an easy alteration of module length and tube materials. The special modular construction facilitates inspection or changing of membranes in a quick and easy manner. The plate-membrane stack operates at pressure compensation (feed to brine). The special hydraulic characteristics ensure safe operation at each pressure stage and at high pressure drops.
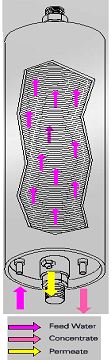
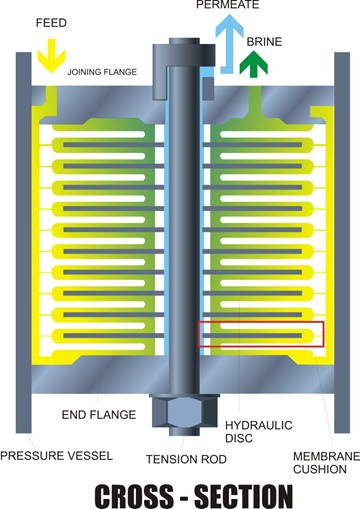
The hydraulics result in a high flow velocity across the membranes at minimum feed flow. The open feed channel over the membrane surface ensures optimal membrane cleaning from fouling deposits.
The extremely short feed water path across the membrane followed by a 180 degree flow reversal, eliminates polarization concentration. Consequently, the PF-Membrane-Module results in minimum membrane fouling and scaling. The permeate drains from the cushion as intermediate layer into the manifold with minimum flow path and with minimum resistance.
A comparison of these membrane modules on the basic parameters is reproduced as below :
Module Configuration
Characteristics |
Plate-Frame |
Spiral |
Hollow Fiber |
Packing density |
High |
High |
Highest |
Permeate flux |
High |
High |
Low |
Pretreatment |
Moderate |
High |
Highest |
Suspended Solids build-up |
Moderate |
High |
Highest |
Having superior constructional features, the PF Modules also score on Operational Aspects and are far simpler to operate due to absence of elaborate stages of pretreatment of raw water.
The PF Membrane Module system can be used with simple backwash Sand filter and cartridge filters of 10 micron. Any permanent wastewater pre-treatment by chemicals at various points is not required. A higher silt density index SDI-blocking factor of 20 only means that the system has to be cleaned less frequently, normally once every 4 weeks.
The cleaning circuit for the PF Module is included in every plant and can be handled simply without any special knowledge demand from operating staff.
The Concord Enviro Module offers additional unique advantages over other types of membranes:
i. Simplified prefiltration: Can smoothly operate with waters having Silt Density Index (SDI) of 20 as against 3-5 tolerated by other membrane modules.
ii. No chemical operating costs: No chemical pretreatment is required for most wastewater applications and also other difficult water qualities.
iii. High recovery rates: High recovery rates (i.e. m3 of Permeate produced/100m3 of feed pumped in) are typically achieved. This means lower energy consumption per unit permeate water produced, and contributes towards lower pumping and maintenance costs in the case of Concord Enviro.
iv. Longer Membrane Life: The Membrane is open channel type and feed water-flow in series. Due to fluid dynamics obtained with this design the suspended solids carried in the feed water do not clog or easily settle over the membrane surface.
It is known fact that makers of hollow fiber or spiral wound membrane system offer a guarantee for the membranes’ life. This will be more or less an optical illusion because this guarantee is based on the operation of wastewater with a SDI-factor less than 3.
Wastewater will be aggressive against the membranes’ modules. But the guarantee will only cover the durability of the membranes’ material against all substances inside wastewater, and not a clogging of a membrane which will be the responsibility of the operator. Therefore such guarantees are of little help or value to the operator and maintainer.
v. Lower membrane replacement costs: Conventional membrane elements are life-sealed at manufacture so the complete element must be replaced at relatively high cost, but the Concord Enviro module system offers the possibility of replacing individual sheets of membrane at a fraction of the cost.
vi. Better Chemical Cleaning: Concord Enviro Module Configurations have design features which minimise fouling to a level where in situ chemical cleaning restores original membrane performance and provides a long operating life; SW and HFF membranes with inherently constricted flow passages are prone to heavy fouling which is only partially handled by chemical cleaning and thus have a pronounced tendency to choke and have limited operating life.
vii. Lower Maintenance Cost: With the Concord Enviro Module, even after the expected life, it is possible to identify the damaged membranes and replace only these membrane envelopes, rather than the total set in the stack. In SW or HFF types, which are factory-sealed for life, the whole module is to be rejected. Thus the replacement cost of membranes is significantly higher for SW and HFF types compared to Concord Enviro.
viii. Low Operating Costs: The above points, reduced pretreatment and longer membrane life, clearly show that the operating costs of the plant are significantly lower than the SW/HFF configurations.
ix. Easy Access to All Components including membranes: Modules can easily be opened up to permit exchange or inspection of each membrane sheet. (This is not possible in SW/HFF, since these are factory sealed)
x. Compact and Modular construction: The unique design offers versatile features like superior flux, smaller foot print, easy handling, ease of scalability, replicability and isolation in case of fault.